Die Battery-Junction-Box (BJB) bzw. Battery Disconnect Unit (BDU) oder Power Distribution Unit (PDU) sind Schalteinheiten, die die Traktionsbatterie mit dem Inverter und Antriebsmotor verbinden bzw. trennen. In Zusammenarbeit mit namhaften Marktanbietern wurden bereits mehrere Einheiten bis zur Serienreife entwickelt. Für die Gesamtauslegung inkl. der thermischen Betrachtungen, das Wärmemanagement bestehen analytische Tools, die durch detailliertere Simulationen ergänzt werden. Know-How besteht zudem in der Auswahl der elektro-mechanischen Komponenten wie Relais/Schütze, Überstromschutz, Vorladewiderstand, Vorlade-Relay und deren elektrische Verbindungen (i.d.R. Stromschienen, Leitungen, Leiterplatten). Ebenso in den Möglichkeiten der Strommessung (Hall-Effekt Stromsensor/LEM, Spannungsabfall am Messwiderstand/shunts, magnetooptische Stromsensoren), Spannungsmessungen und Diagnosemöglichkeiten. Zudem in der Ausführung der Spannungsabgriffe für die Überwachung/Intelligenz durch Kabel oder Stanzgitter und geeignete Kontaktierelemente oder -klammern unter Berücksichtigung der Anforderungen wie Vibrationsbelastbarkeit und Wärmeausdehnung.
Schalten und Trennen von Strömen
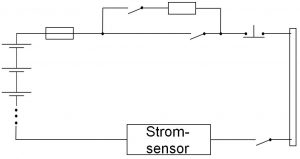
Battery-Junction-Box, dargestellt ist ein typischer Hochvolt/Hochstrompfad bis zum Hochvolt Steckverbindersystem
Die wesentliche Funktion ist das Schalten von Strömen. Herzstück der Battery-Junction-Box sind dadurch die Schalteinheiten, durch Halbleiter-Schaltungen/Solid-State-Relais oder Power Contactoren realisiert. Um die Schaltströme (inrush currents auf Grund von System-Kapazitäten) beim Hochfahren des Systems auf zulässige Beträge zu begrenzen werden Vorladeeinheiten vorgesehen. So werden Beschädigungen durch Lichtbogenbildung oder Kontakt-Verschmelzung in mechanischen Schalteinheiten vermieden. Wird keine galvanische Trennung gefordert, können Relais auch als MosFET-/Halbleiter-/Semiconductor-Schaltung als solid-state relay ausgeführt werden.
Eine besondere Herausforderung stellt der Überstromschutz, das sichere lückenlose Abschalten auch in Fehlerfällen dar, für das i.d.R. Überlast-Komponenten z.B. Schmelzsicherungen, Switches, Pyroswitches, Breakers, Relais oder Solid-State Power Controller (SSPC) integriert werden. Für das sichere lückenlose Abschalten werden auf Systemebene der Battery-Junction-Box die Komponenten nach den Fahrprofilen und den Betriebsbereichen dimensioniert und auch die einzelnen Komponenten aufeinander abgestimmt.
Die Intelligenz des Systems
Das Batteriemanagementsystem (BMS) ist die Steuereinheit des gesamten Systems. Sie sammelt Daten von den Batteriemodulen (z. B. Spannungen und Temperaturen der Batteriezellen) und vom Stromsensor und verwendet diese Daten für Batteriezustandsberechnungen (z.B. SOC, SOH, SOF). Darüber hinaus steuert das BMS das Balancing der Batteriezellen, die Power Contactoren, unterstützt die Diagnosemöglichkeiten (inkl. Isolationsmonitoring) und kommuniziert über den CAN-Bus mit übergeordneten Steuereinheiten.
Das Thermomanagement
Verlustleistungen innerhalb der Battery-Junction-Box müssen minimiert werden, denn sie führen zur Erwärmung der Komponenten und der elektrischen Verbindungen. Daher sind thermische Betrachtungen und thermische Simulationen erforderlich, bei Berücksichtigung der Komponenten und Kennlinien, der Übergänge (elektrisch und thermisch), der Wärmeleitungen und Wärmekapazitäten. Unzulässige Erwärmungen können zur vorzeitigen Alterung von Komponenten, der elektrischen Verbindungen und Degradierung von Werkstoffen wie Isolationswerkstoffen oder Beschichtungen führen. Umgekehrt bieten sich Möglichkeiten zur Entwärmung, zur Minimierung von Temperaturen (Derating-Kurven) und zur Steigerung der Lebensdauer von elektronischen Komponenten/Hardware-Bauteilen wie Relais, Widerständen oder Steckkontakten.
Die Optimierung der Verlege-Wege, Layout und Routing (durch NV und HV-Leitungen) ist insbesondere aus Sicht der elektromagnetischen Verträglichkeit (EMV) und Temperaturentwicklung/Entwärmung entscheidend. Für die erste Optimierung/für die Vorauslegung bieten sich vereinfachte analytische Betrachtungen der wesentlichen Größen und Einflussgrößen an. Nach den Design-Entwürfen folgen Struktur-, Thermodynamische- und EMV-Simulationen (z.B. Wärmeentwicklung, Wirksamkeit der Entwärmungskonzepte) und die Verifizierung.
Die elektrische Verbindungen und Verbindungstechniken
Elektrische Verbindungen können durch verschiedene Möglichkeiten realisiert werden
- Stromschienen: zur Kostenoptimierung bieten sich innovative Herstellungskonzepte, kostenoptimale nicht zur Wiskerbildung neigende Beschichtungen (Korrosionsschutz durch Beschichtung vs. Passivierung vs. lokale Kontaktaufbereitung) und Synergien mit der Reinigung, der Sauberkeitsanforderungen an die Komponenten. Link und weitere Details zum Thema Stromschienen und bus-bars
- Leitungen, Crimp-Verbindungen und Steckverbindungen
- Leiterplatten (PCB, Hochstrom-PCB, PCB+Wire-Kombinationen, PCB+SMD-soldered busbars)
Jede dieser Lösungen hat Stärken, die wir für den spezifischen Einsatzfall bewerten.
Wir unterstützen im Design bis zum Herstellungsprozess. Im Design halten wir die Anforderungen und Funktionen im Fokus. Auf Grund der Materialkosten, der Gewichts- und Volumenanteile elektrischer Verbindungen bietet sich zudem hohe Optimierungspotentiale. Die Optimierung beinhaltet z.B. die Werkstoffwahl (Kupfer, Kupferlegierungen vs. Aluminium, Aluminiumlegierungen), die Form (voll vs. Litze/Geflecht, rund- vs. Flachmaterial), Korrosionsschutz (Beschichtung vs. Passivierung), innovative Herstellungskonzepte (Folge-Verbund vs. Biegen und Ablängen vom Halbzeug/Flachmaterial-Coil).
Je nach Anforderung werden Hochstrom-Verbindungen hinsichtlich einheitlicher geringer Widerstände optimiert. Dadurch werden die Batterien gleichmäßiger entladen oder geladen. So kann im Betrieb mehr Energie entnommen und beim Laden muss weniger korrigiert/balanced werden. Leistungshalbleiterschaltungen werden hinsichtlich niederinduktiven Verbindungen und Verbindungstechniken optimiert. Ebenso hinsichtlich elektromagnetischer Verträglichkeit (EMV/EMI). Bei Anforderungen an Signal-Integrität bei höheren Datenraten beachten wir zudem Symmetrieanforderungen von Pinpaaren, designen Pin-Breiten und Mäander für optimale Laufzeiten als auch Moden-Konversion-Parameter.
Die Isolation/Isolationskoordination kann z.B. durch die Kunststoff-Gehäusestrukturen/Tragestruktur, Kunststoff-Klappscharniere/Clips, Ummandelung/Umspritzen/Umgießen/Tauchverfahren/Pulverbeschichtung, Schrumpfschlauch, Isolierfolien, Lackierungen (vgl. Kupfer-Lackdraht) und deren Kombinationen bzw. Mehrschichtsystemen erfolgen.
Weiteres Potential liegt in den Verbindungstechnologien (Formschluss, Schraub- vs. Steckverbindung). Eine Voraussetzung für einen robusten langlebigen elektrischen Kontakt ist die mechanische und chemische Stabilität des Kontaktes. Neben dem Know-How für die Auslegung haben wir auch ergänzende Prüftechniken aus den Bereichen der Tribologie wie Verschleiß- oder Reibkorrosionsprüfstände oder auch der Verbindungstechniken wie Schraubfall-Analyse und Ermittlung des Weiterdrehmoments.
Gehäuse, tragende Strukturen und Massekonzepte
Unsere Stärke liegt in den systemübergreifenden Betrachtung der zahlreichen Funktionen, in der Definition der Anforderungen und Ableitung von Akzeptanztests, sowie in der Erarbeitung und Bewertung von Design-Lösungen. Das beinhaltet bspw. das Batteriegehäuse-Design, Trage-Strukturen, Dichtungen, elektrische und mechanische Verbindungen, wiring harness, Konnektoren bis zur Kabelkonfektion, Hochvolt- und Kommunikations-Schnittstellen, Temperierung/Entwärmung, Gehäuse-Druckausgleich, Kondensat-Vermeidung, IP-Dichtheit/Schutzklasse und EMV-Dichtheit, Schirmungs- und Massekonzepte (Grounding).
Die Abstimmung dieser System-Komponenten inkl. des Schirmungs- und Grounding-Konzepts ist entscheidend um geforderte Dämpfungskennwerte des Frequenzbereichs und damit die elektromagnetische Verträglichkeit/EMV-Anforderungen an das System z.B. einer Battery-Junction-Box (BJB) zu erreichen.
Weitere Information erhalten Sie gerne in einem unverbindlichen und persönlichen Gespräch: Link zur Kontakt-Seite